Fasteners and Machining: Enhancing Sturdiness and Performance in Production
Fasteners and Machining: Enhancing Sturdiness and Performance in Production
Blog Article
Browsing the Globe of Fasteners and Machining: Approaches for Accuracy and Rate
In the intricate realm of bolts and machining, the mission for accuracy and rate is a continuous challenge that demands thorough interest to detail and tactical preparation. From understanding the varied range of fastener types to choosing ideal materials that can withstand extensive needs, each step in the procedure plays a crucial function in achieving the desired result.
Understanding Bolt Kind
When selecting fasteners for a job, comprehending the numerous kinds available is essential for guaranteeing ideal efficiency and dependability. Bolts come in a large range of types, each made for specific applications and needs. Screws are made use of with nuts to hold products with each other, while screws are versatile bolts that can be made use of with or without a nut, depending upon the application. Nuts, on the various other hand, are inside threaded fasteners that mate with screws or screws, offering a secure hold. Washers are important for dispersing the load of the fastener and stopping damages to the product being secured. In addition, rivets are long-term bolts that are excellent for applications where disassembly is not needed. Recognizing the distinctions in between these bolt kinds is necessary for selecting the right one for the work, making sure that the link is strong, sturdy, and trusted. By selecting the suitable fastener type, you can enhance the efficiency and longevity of your project - Fasteners and Machining.
Selecting the Right Products
Understanding the importance of selecting the right materials is critical in ensuring the optimum efficiency and dependability of the selected fastener kinds reviewed formerly. When it pertains to fasteners and machining applications, the product selection plays a vital function in determining the total stamina, toughness, deterioration resistance, and compatibility with the designated atmosphere. Various products supply differing residential or commercial properties that can significantly affect the performance of the bolts.
Common materials made use of for bolts include steel, stainless-steel, titanium, light weight aluminum, and brass, each having its one-of-a-kind strengths and weaknesses. Steel is renowned for its high strength and resilience, making it ideal for a vast array of applications. Stainless steel uses superb rust resistance, perfect for atmospheres vulnerable to moisture and chemicals. Light weight aluminum is lightweight and corrosion-resistant, making it suitable for applications where weight reduction is critical. Brass is typically picked for its aesthetic allure and exceptional conductivity. Titanium is recognized for its exceptional strength-to-weight proportion, making it ideal for high-performance applications. Selecting the ideal material entails taking into consideration factors such as toughness needs, ecological problems, and budget constraints to make certain the preferred performance and long life of the fasteners.
Precision Machining Techniques
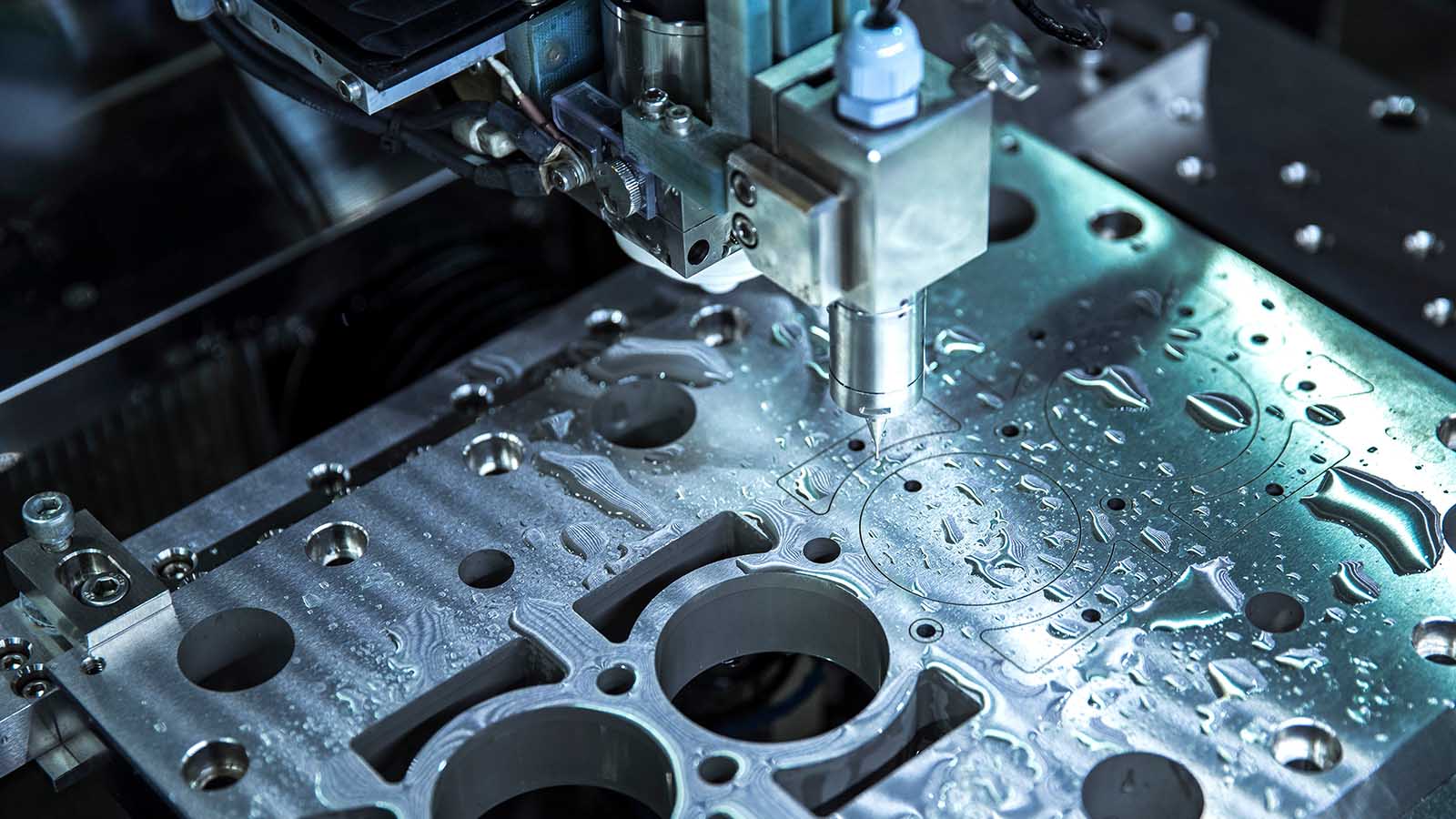
Along with CNC machining, various other accuracy strategies like grinding, turning, milling, and boring play vital functions in fastener production. Grinding helps achieve fine surface finishes and limited dimensional tolerances, while transforming is commonly utilized to create round parts with specific sizes. Milling and exploration procedures are necessary for shaping and producing holes in fasteners, guaranteeing they fulfill specific specifications and function properly.
Enhancing Rate and Performance
To maximize bolt production procedures, it is important to simplify operations and carry out efficient methods that click here to read enhance accuracy machining methods. One key strategy for enhancing speed and efficiency is the application of lean manufacturing concepts. By minimizing waste and concentrating on continual improvement, lean methods help remove traffic jams and enhance workflow. Additionally, purchasing automation modern technologies can dramatically improve production speed. Automated systems can manage recurring tasks with accuracy and rate, allowing workers to concentrate on more complicated and value-added activities. Taking On Just-In-Time (JIT) stock administration can additionally improve effectiveness by making certain that the ideal materials are offered at the appropriate time, decreasing excess inventory and reducing lead times. Additionally, promoting a culture of partnership and communication amongst staff member can improve total performance by promoting transparency, analytical, and technology. By incorporating these methods, manufacturers can achieve a balance between speed and precision, ultimately boosting their competitive edge in the bolt sector.
Quality Assurance Procedures
Implementing rigorous quality control actions is critical in guaranteeing the reliability and uniformity of bolt products in the manufacturing process. Quality assurance actions incorporate numerous phases, beginning with the option of basic materials to the final assessment of the ended up fasteners. One basic aspect of quality assurance is conducting extensive product examinations to validate compliance with specs. This involves evaluating elements such as material strength, structure, and longevity to assure that the bolts meet industry requirements. Furthermore, monitoring the machining refines is vital to support dimensional precision and surface area coating high quality. Making use of sophisticated technology, such as automated examination systems and accuracy measuring devices, can my company improve the accuracy and effectiveness of quality assurance procedures.
Routine calibration of equipment and equipment is critical to preserve uniformity in production and guarantee that fasteners satisfy the required tolerances. Executing strict protocols for identifying and dealing with non-conformities or flaws is vital in stopping substandard items from entering the market. By developing a thorough quality assurance framework, manufacturers can support the reputation of their brand name and deliver fasteners that satisfy the highest possible requirements of efficiency and durability.
Verdict
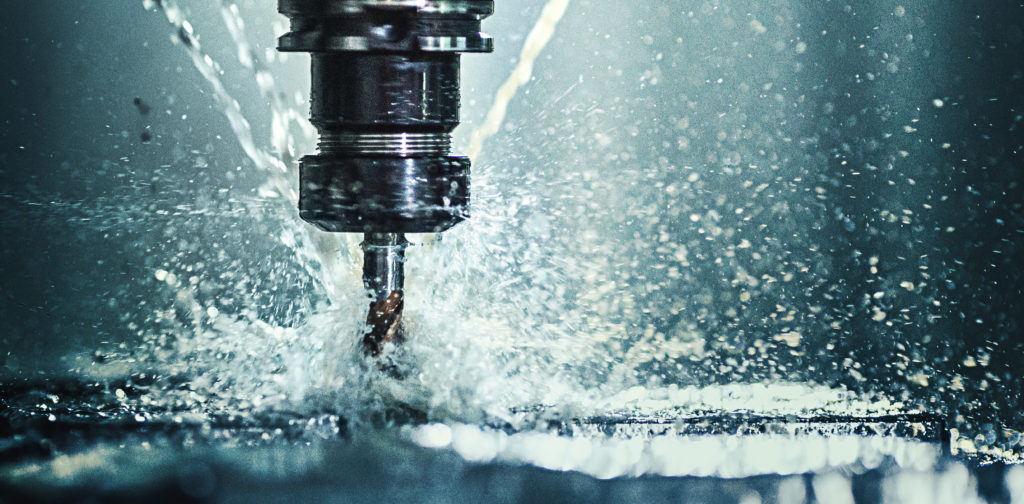
In the detailed world of fasteners and machining, the pursuit for accuracy and rate is a continuous challenge that requires thorough attention to information and strategic planning. When it comes to fasteners and machining applications, the material selection plays a vital duty in establishing the total toughness, durability, corrosion resistance, and compatibility with the designated environment. Precision machining includes different innovative approaches that ensure the tight tolerances and requirements required for fasteners.In addition to CNC machining, various other accuracy techniques like grinding, turning, milling, and exploration play essential duties in fastener manufacturing.To optimize fastener production procedures, it is important to enhance procedures and implement effective strategies that enhance accuracy machining techniques.
Report this page